Ferrovial is working to create risk-free environments for its employees and users, based on the premise that there is no accident that may not be avoided.
The Health and Safety strategy that Ferrovial has been developing in recent years, combined with the firm commitment of both management and all employees, has made it possible to reduce the company’s accident rate drastically. Quoting just one figure is enough to corroborate its efficiency; the rate of accidents involving leave of absence has dropped by 42% since 2014.
Based on the premise that no accident is unavoidable, Ferrovial’s Health and Safety strategy is founded on six pillars: risk assessment and the development of systems of control; compliance with legislation; efficient and effective communications in order to generate a culture of safety throughout the whole company; the training and involvement of workers; a system of reporting which enables us to measure and evaluate our safety performance; and innovation, introducing new action guidelines, technologies and measures.
Based on these principles, each business unit develops a range of initiatives working towards a shared goal, Target Zero. Many of these have won awards.
Attaining the Target Zero goal
Ferrovial Agroman has introduced a corporate system of health and safety in accordance with OHSAS 18001 certification, which is currently the main international standard in this area. The system establishes a series of minimum health and safety standards and procedures, which are applied in all areas of the business, regardless of country, generating a corporate safety culture across all projects.
Furthermore, Ferrovial’s construction subsidiary has launched a number of programmes (SAFE, BIP, LIFE) in which observation on the part of employees, and their participation in improving safety conditions, are key. In June 2018, the InSite Prevention Module was completed, bringing together all of the functions necessary for comprehensive safety management on construction projects in one application, with particular emphasis on the analysis of indicators and the digitalisation of the information generated.
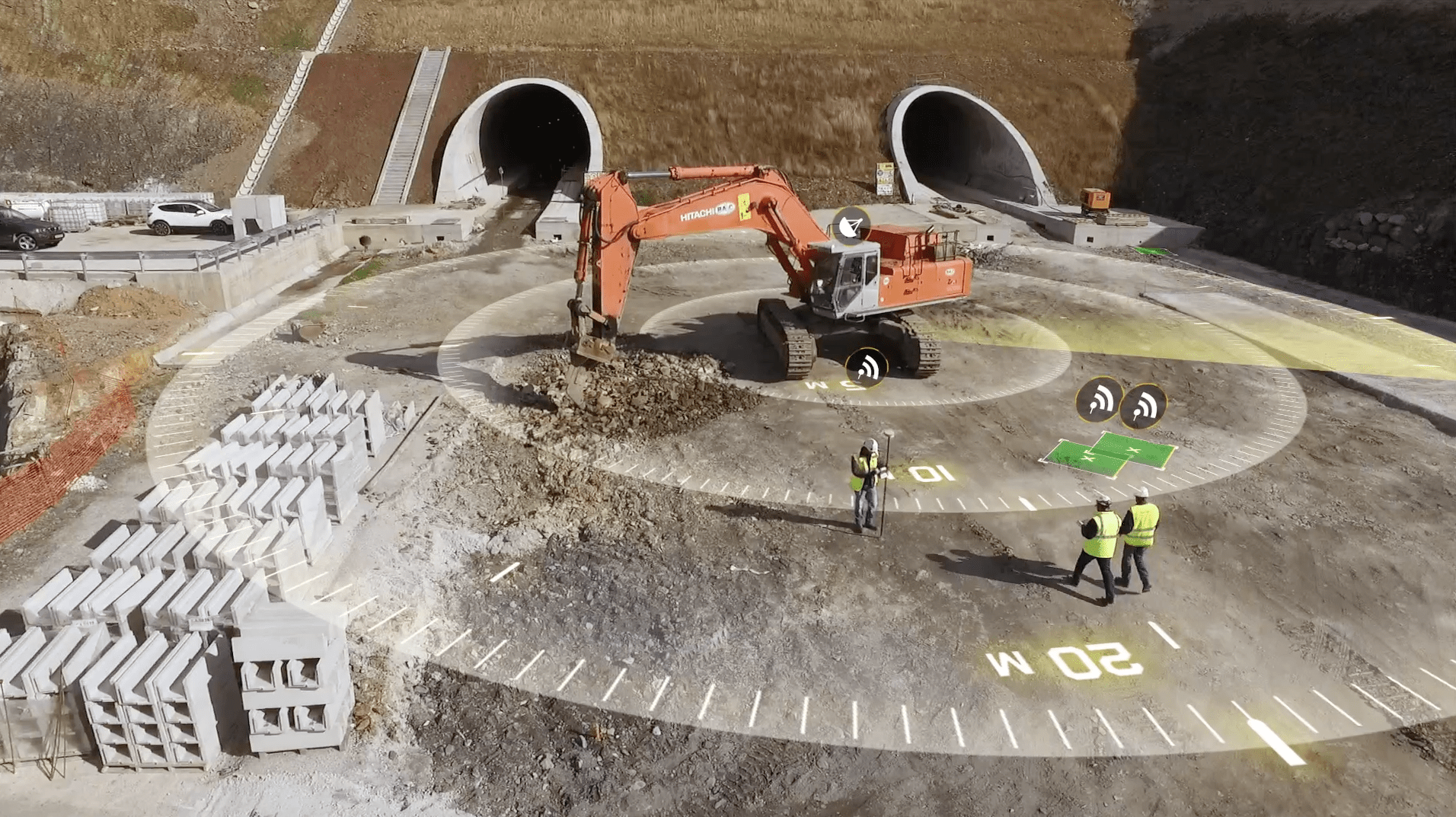
With the aim of achieving Target Zero, Ferrovial Agroman is incorporating the latest technologies in IoT (Internet of things) in its construction projects. The devices developed for the “Risk Reaction” tool allow us to manage site access in an automated manner, refusing entry to workers who do not comply with the required safety measures. They also enable us to remotely verify whether the worker is trained for using a specific piece of machinery or equipment and, by pressing a button, to alert to any emergency for early attention. Moreover, the “Warning Presence of People” system warns of the risk of being run over in the vicinity of heavy machinery, notifying the driver and the worker that they are within the machinery’s radius of action.
Ferrovial Services, meanwhile, is committed to the introduction of new technologies in order to create a safer working environment. One of these is wearable technology, which through the installation of biometric and location sensors makes it possible to monitor the physical activity and location of workers. The analysis of the data collected by these devices enables us to identify situations that might generate stress or fatigue in our professionals, and to adopt measures to deal with them. This technology has been applied in the highway maintenance contract that Amey manages in the northeast of England.
In the same country, the Ferrovial Services subsidiary has tested the benefits of virtual reality in risk prevention training. To be specific, it was applied to driver training. One simulator recreated driving conditions involving fatigue, with the aim of workers learning to identify such situations and how to deal with them. This is key to accident prevention given that tiredness is one of the factors with the greatest impact on occupational accident rates.
As well as wearable technology and virtual reality, Ferrovial Services is making use of mobile applications in its highway maintenance contracts: In Poland, FBSerwis has developed and introduced SKOPI, a tool enabling users to issue notifications that works are being carried out at specific locations on the Polish road network. SKOPI works as part of Yanosik, one of the most popular apps used by drivers in the country. With this initiative, the company is attempting to raise awareness of the danger involved in roadworks and the risks faced by maintenance professionals when traffic regulations are not complied with.
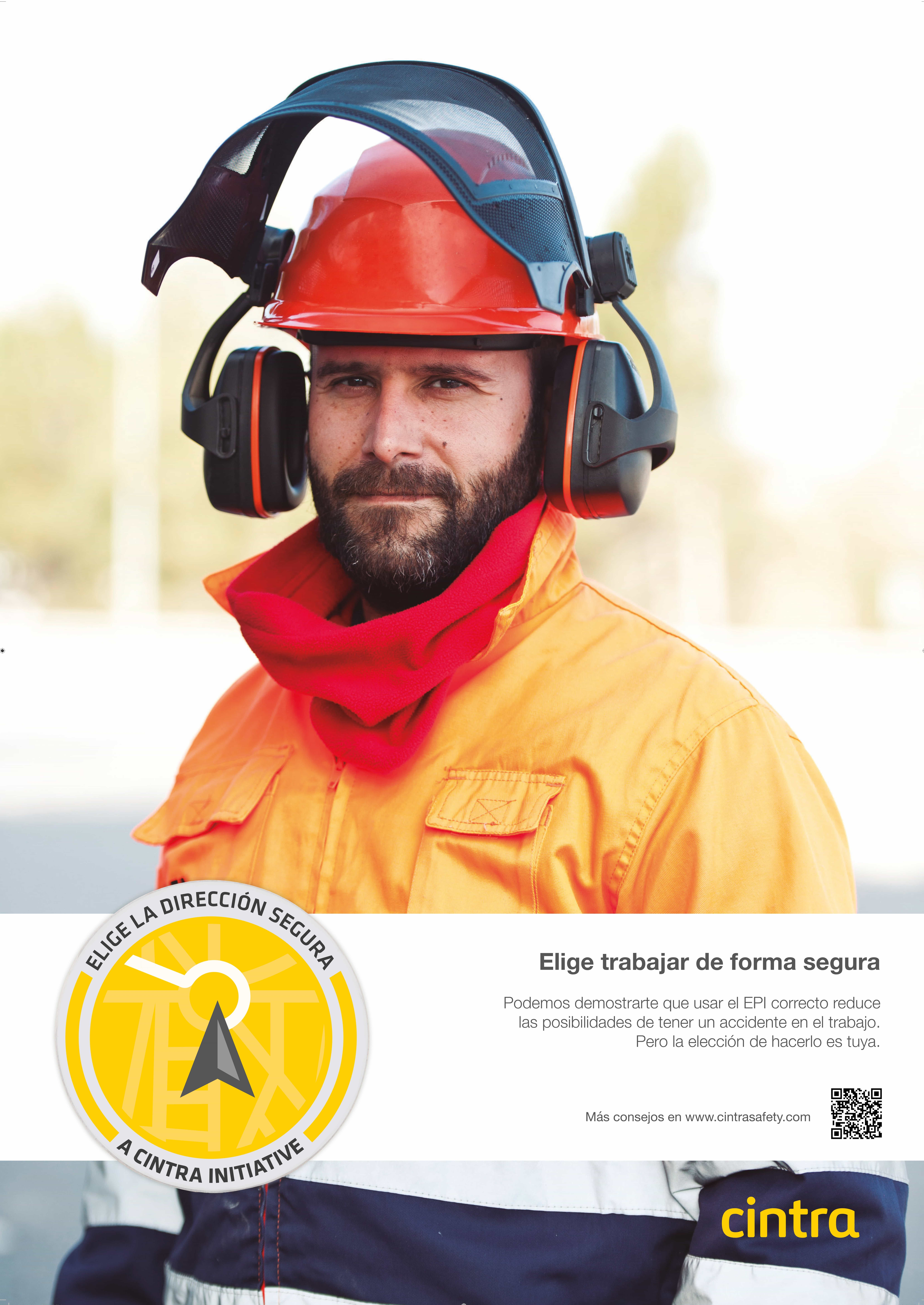
It was precisely this concern for the safety of workers and drivers that acted as the driving force behind the “Choose the Safe Way” campaign in Cintra. On the one hand, it aimed to emphasise the fact that for workers at the Ferrovial motorway subsidiary there can only be one way of doing things – the safe way – while on the other hand it stressed the fact that motorways constitute the safest way of getting around.